Broad and Valuable, But Not Always Applicable, Ideas in ‘The Goal’
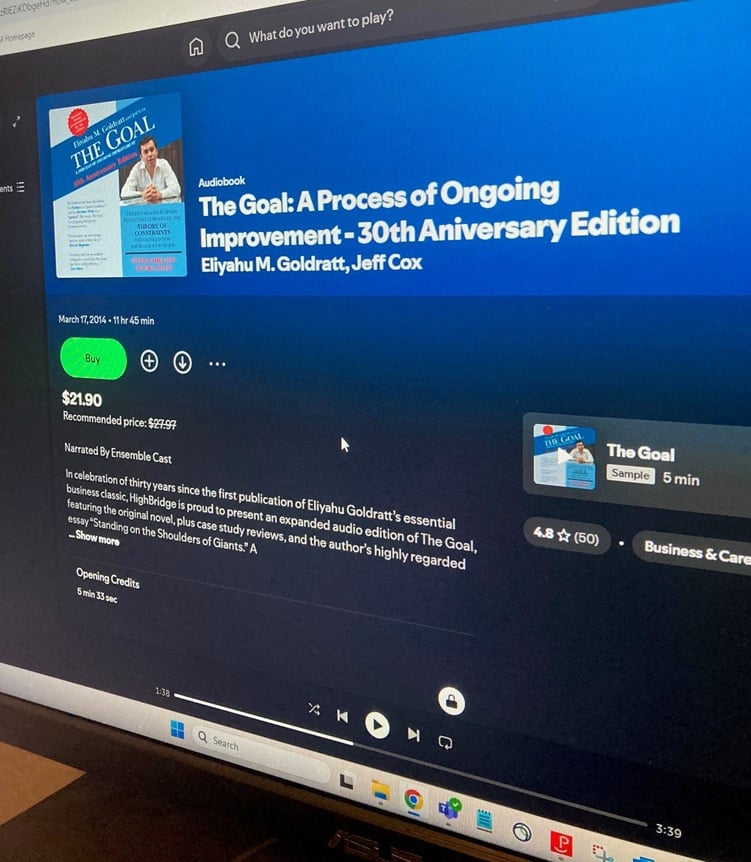
The book The Goal is often touted as a great example of a business book that makes a difference in the lives of supply managers and other professionals.
Written by Eliyahu M. Goldratt and Jeff Cox in 1984 — and revised numerous times — it still is a perennial favorite and has held a place on Time’s list of the top 25 most influential business management books — and for good reason. Many of the lessons detailed are broad and can, therefore, be edited to fit the confines of any industry. The core ideas presented are extremely valuable.
However, given growing geopolitical tension, supply chain disruption, technological development and evolution in processes, how does the book hold up 40 years after it was written?
The Theory of Constraints
In The Goal, the authors communicate vital lessons for organizations through the adventures of Alex Rogo, a plant manager who attempts to improve his factory’s discrete manufacturing process.
The book places the most importance on Goldratt’s Theory of Constraints (TOC) — specifically, how the rate of a process is often determined by bottleneck steps. It is imperative for organizations to understand this concept to ensure they do not spend resources and time on increasing local optimums.
For example, there is no use in increasing the capacity of Machine A, which can cut 20 parts per minute, to 30 parts per minute if the parts are doomed to stockpile in front of Machine B, which can only package 10 parts per minute.
This example (as well as the examples used in the book to explain local maximums and bottlenecks) can be scaled up to be an inter-departmental problem. Consider General Motors (GM) in the 1980s and ’90s. As authors James P. Womack, Daniel T. Jones and Daniel Roos explain in their book, The Machine That Changed the World: The Story of Lean Production, then-CEO Roger Smith reflected that the early days of GM were spent improving local efficiencies (individual departments in this case) rather than finding and curing systemic bottlenecks such as a misaligned production flow.
The Goal directs companies to where time and energy should be spent, a lesson that an industry giant can confirm the importance of. That’s something that is always applicable.
Dependent Events and Statistical Fluctuations
Consider the importance of dependent events and statistical fluctuations, another point made in the book.
Goldratt and Cox refer to such statistical fluctuations as setup times and variances in output within a manufacturing process, with dependent events being consequent stages in a manufacturing process that are subject to statistical fluctuations due to preceding stages. This is reminiscent of the bullwhip effect, which occurs due to variances in consumer demand and the retailer’s reaction to it. When the retailer orders more than is needed/expected, the order amount is increased dramatically upstream due to overreaction and dependency.
Supply chains experiencing the bullwhip effect face inefficiency and increased costs.
By understanding the authors’ intent, TOC can be applied to much larger contexts while making connections to concepts or events (like the bullwhip effect) that occur outside of the company.
Defining TOC
The broad applicability of The Goal is best demonstrated through TOC’s five-step process and a focus on three measurements: throughput, inventory and operational expense. The five-step process involves (1) identifying the constraint, (2) exploiting it, (3) subordinating everything to the constraint, (4) elevating the constraint’s performance and (5) repeating the process.
A study of 100 companies with TOC implementation found, on average, a 69-percent reduction in lead times, 50-percent reduction in inventory and 58-percent increase in throughput. The results of the study demonstrate TOC’s potential if applied correctly. Targeting limiting factors can foster significant and continuous advancements.
A difference should be made, however, between valuable ideas and universally applicable ideas. The aforementioned lessons are valuable no matter the industry, but they should not always be applied. Why? Companies may have organizational goals that require a non-TOC supply chain strategy.
For example, a company that would like to focus on resilience and adaptability to market changes might focus on having a decentralized supply chain for better local responsiveness and decision-making. This makes it difficult to implement TOC, which is a strategy that emphasizes centralized decision-making. Additionally, those focused on maintaining inventory levels higher than their industry average are more likely to spend more resources on long-term plans, whereas TOC focuses on short-term improvements.
The Non-Discrete Difference
Consider non-discrete manufacturing processes, which involve products that are not easily countable and are usually produced in bulk through batches. The nature of non-discrete manufacturing settings makes bottleneck identification difficult, thereby making all consequent steps and advice difficult to apply.
In The Goal, Rogo’s bottlenecks are clear due to the discrete manufacturing setting: Individual units are made through distinct steps and machines. However, non-discrete utilizes continuous and batch-based processing, which makes finding bottlenecks more difficult because of the fluidity. Plus, non-discrete manufacturing is usually used for producing a homogenous “mix,” which makes the three TOC metrics difficult to define and apply.
TOC would cause more headaches than solutions to those in a non-discrete setting. The bottleneck identification and resolution process would be met with multiple challenges, rendering it impractical.
A Closer Look
Fruitastic punch, a hypothetical product, is made with equal parts orange, cherry and blueberry juice. The juices are poured together into a large vat and blended. After some time, the mixture is transferred to another vat for pasteurization to eliminate any bacteria from the mixture. From there, Fruitastic is cooled, bottled and packaged to send off to customers. Throughout this entire process, pasteurization is the step that takes the longest to complete.
Following TOC’s five-step process, system constraints are identified first. In a discrete process, workstations would be identified and evaluated. However, since Fruitastic production is designed to be continuous, the stages are interlinked, which means production rates are determined by equipment design and capacity. For example, if both the mixing and pasteurization vats are constantly operating at their fixed capacities, then the bottleneck would be the slowest rate in the system rather than an identifiable resource as it would be in the case of discrete manufacturing processes.
The second step: Few realistic options are available to exploit the system constraint. Currently, the pasteurization step requires the most amount of time; can that be changed? It is a critical stage that adheres to strict temperatures and times for quality and safety reasons. Increasing the speed and reducing the time required for this step could compromise the product. (In discrete manufacturing, on the other hand, production speed can be increased without harming the result.)
The third step: Subordination could cause redundancy in Fruitastic’s manufacturing process. Since mixing, pasteurization and packaging are synchronized to operate at a uniform rate to avoid contamination and quality inconsistencies, there is no way to alter the timing or prioritization of processes. Using a buffer of unpasteurized fruit punch would be impractical due to food safety and freshness issues.
Step 4: There will be many challenges when attempting to elevate the constraint. Most will be due to cost, as the only way to elevate the pasteurizing process would be to add capacity through purchasing a new tank. Consequently, the entire production line would have to be upgraded so pasteurization vats could be used simultaneously.
Step 5: Industry quality and safety standards restrict Fruitastic’s (and many other non-discrete manufacturing processes with such products as food and beverages, chemicals and pharmaceuticals) flexibility for iterative improvement. Specifically, regulatory compliance may not allow Fruitastic to decrease its processing times, temperatures or equipment. This makes it difficult to adapt processes as easily as TOC suggests.
Still Applicable, Yet …
Despite the specifics of TOC failing to serve Fruitastic and other non-discrete manufacturing processes as efficiently as discrete ones, professionals in both areas should make a point to understand Goldratt’s and Cox’s suggestions.
Even though TOC is hard to apply to non-discrete, the core idea of wanting to make your process more efficient is an imperative for most organizations in today’s disruptive environment. Goldratt set out to teach one part of the process can’t be optimized without considering how it will impact the others: a concept all supply chain professionals should keep in mind.
Still, the age of this book is relevant, as much has changed in the profession since its publication. At one point, Rogo realizes that he’s constantly reacting to new bottlenecks and constraints, which worries him. He’d be happy to learn that, depending on the study, as much as 78 percent of supply chain organizations have adopted artificial intelligence (AI) to help form proactive and predictive strategies.
Additionally, AI is helping companies make more informed decisions and providing them with greater visibility within their processes, which reduces the dependency on trial-and-error as emphasized in The Goal.
Globalization is much more common now than in the 1980s, which puts supply chains at greater risk of disruptions caused by international events. Thus, there’s a higher importance placed on resilience and adaptability as opposed to just focusing on efficiency.