Geographic Diversification in Manufacturing: A Risk Management Imperative
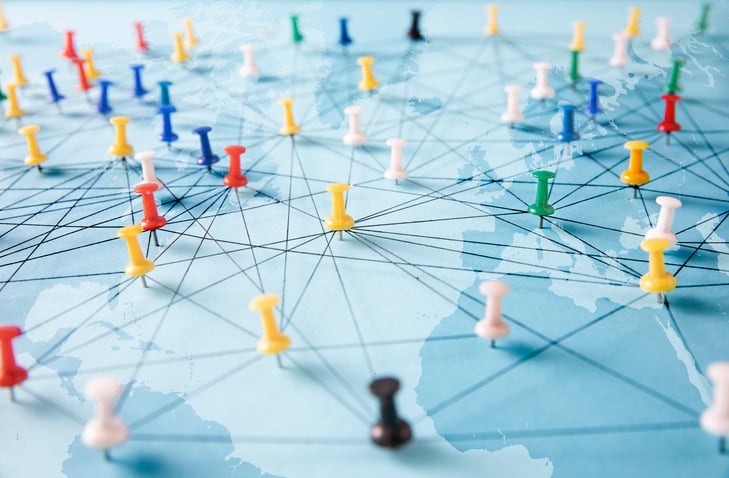
In late September, Hurricane Helene devastated the Baxter manufacturing facility in Marion, North Carolina, taking offline its capacity to manufacture IV fluids and other critical medical materials.
Although the facility has resumed pre-Helene production levels, this unexpected supply chain disruption once again calls attention to the importance of geographic diversification in supply chain management.
It wasn’t that long ago that supply chain and logistics operations worldwide were caught off-guard as COVID-19 swept through China, then the rest of the world. Manufacturing plants clustered in China closed. Ports struggled to operate at normal throughput, with lengthy queues outside the ports of Los Angeles and Long Beach in Southern California.
A natural disaster — Hurricane Helene — has further disrupted supply chains; its damage to the Baxter plant significantly worsened already existing hospital shortages of saline, along with other solutions used in treating patients with kidney failure.
The Hidden Cost of Geographic Concentration
Decisions to concentrate manufacturing or distribution capacity in one area are often justified by economies of scale, simplified logistics, reduced inventory and easier management oversight. This view is somewhat short-sighted, given that a localized event — whether a natural disaster, political unrest or even a prolonged power outage — can bring production to a complete halt, potentially devastating the entire supply chain.
Hurricane Helene’s effect on the hospital supply chain demonstrates how geographic concentration can transform a local disaster into a global crisis. For any manufacturer, sudden loss of production capacity due to supply chain interruption can have lasting consequences, including:
- The loss of market share to competitors that can continue production
- Loss of loyal customers who move their business to a competitor
- Unplanned recovery costs
- Increased insurance premiums
- Breached contracts and associated contract penalties
- Loss of long-term revenue due to the attrition of the company’s customer base.
Network Modeling: A Data-Driven Approach
Geographically dispersing an organization’s production capacity and/or suppliers can be a benefit for supply management practitioners. Network modeling can — and should — be used in determining the best locations for plants, given the potential impact of supply shutdowns on inventory levels and customer service.
Factors to consider include:
- Transportation costs and times
- Labor costs and availability
- Local regulatory environment
- Natural disaster risk profiles
- Political stability indexes
- Proximity to key markets and suppliers
- Tax implications and incentives.
The modeling process is designed to arrive at an optimized manufacturing structure that balances costs, service and risks.
Approach Diversification Strategically
A client company, an agricultural segment leader, demonstrates the value of such a model. The organization had been using the Port of Houston for a substantial portion of its Gulf Coast and East Coast imports.
But a major hurricane had been predicted to strike Houston within 10 years, calling for diversification. As a result of the analysis, changes were made to the client’s distribution network, incorporating the use of additional East Coast ports.
Geographic diversification of manufacturing capacity is no longer optional in today’s volatile business environment. While diversification may result in higher operational costs, these can be thought of as insurance premiums against catastrophic disruption.
The key is to approach diversification strategically, using network modeling and simulation to more closely evaluate the future-state network.