Logistics Transformation Targets People and Technologies
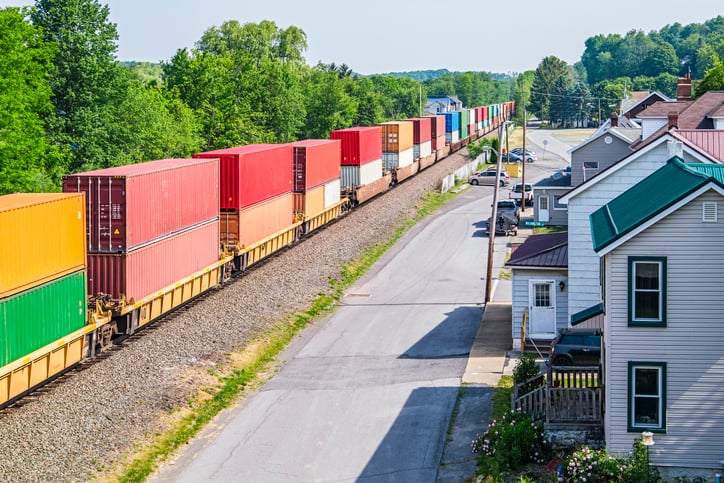
Transportation, freight and logistics companies have had to manage myriad disruptions over the past few years, from labor issues, challenges in delivery and supply, the coronavirus pandemic, new technologies, and changing consumer and customer preferences.
At last month’s Supply Chain USA 2024 event in Atlanta, two freight companies talked about transformation in the logistics space.
Putting People First
After the pandemic, CSX set out to transform its workplace culture to promote employee engagement and collaboration and become more customer-centric.
COVID-19 led the rail-based transportation company, like other railroads, to lay off employees due to the economy shutting down. It wasn’t long before they were called back, but many didn’t return, CSX CEO Joseph Hinrichs said during the event, which was hosted by Reuters Events, part of London-based Reuters News & Media Ltd.
It takes six months to train a conductor, and it took several years for CSX to build back its workforce. That and other challenges, like several years of labor negotiations and other pandemic impacts, “shocked us into realizing how important it is to be an employer of choice,” Hinrichs said during “Leveraging Innovation to Drive Customer Success and Build Retention.”
So, the company decided to take a new approach and embarked on a mission, he said, “to bring about that culture where every employee feels valued, appreciated, respected, included and listened to, and we use those words intentionally and often to make sure we’re setting the right framework for our leaders and how we treat people.” Having an engaged and aligned workforce also would enable the company to run better and more efficiently, he said.
The effort resulted in greater internal and external collaboration, Hinrichs said. The company is working with the Georgia Port Authority to develop inland ports to be able to quickly move goods away from the Port of Savannah to reduce port congestion, make operations more efficient and lessen the impact on the community, he said.
Putting Tech on the Tracks
Technological advances, particularly artificial intelligence (AI), also play a role in CSX’s customer-centric strategy. Some of the basic architecture of railroads is more than 100 years old, Hinrich’s said. “What we’re trying to do is leverage technology, whether machine learning, AI, camera systems and the like, to enhance the capabilities we have and also to supplement the work of our employees on inspecting,” he said.
Safety is paramount to CSX, which utilizes AI to check the temperature of the bearings on the steel wheels to ensure they don’t overheat, which would cause the train to derail. Temperatures are tracked every 15 miles; an algorithm checks for trends and issues, he said.
AI is also instrumental in the company’s sustainability efforts. Rail is a more environmentally efficient way to move goods than trucks, Hinrichs said. To become even more environmentally friendly, the company has implemented a variety of programs that include testing biodiesel fuels, hydrogen as a fuel, and electric locomotives.
“The opportunity we have is to run better and more efficiently and to be more customer-centric to get more business on the rail and off the trucks,” he said.
Uber Freight
The AI equation is changing transportation and delivery, said Lior Ron, founder and CEO of Uber Freight, a business unit of Uber Technologies. “I think it’s very clear that we are facing a once in a lifetime transformation for the way we operate logistics and supply chain,” he said.
During the session “Harnessing the Power of AI: How to Transform Your Supplty Chain,” Ron said logistics is inherently an optimization challenge. “At the end of the day, we (are trying to) optimize between service and cost. We’re trying to optimize our network,” he said. “We’re trying to improve our output.”
Using AI to automate and gain visualization can enable the logistics companies to allow their workforce to focus on higher-level tasks while reducing operating expenses. For the past eight years, Uber Freight has been working to digitize all aspects of the entire logistics system.
Now, Ron said, the company manages US$18 billion in freight under management. It has more than 6,000 customers on its network. “We were able to build the largest digital freight company assembled in the industry. We have more than 2 million truck drivers on the platform — that’s like over two-thirds of over the road drivers in the U.S. — who have downloaded our app and connected with our web tools.”
For Uber Freight, machine learning and AI enable more accurate and efficient shipping information and processes, Ron said. Weather patterns, supply and demand, and market rates are just some of the factors that are analyzed. In the logistics industry, they are being tapped to change the face of deliveries, as generative AI is being used to train self-driving trucks, he said.
“Generative AI is the next frontier for logistics and the next frontier for supply chain,” Ron said, adding that AI use starts with (1) education, (2) identification of where it makes the most sense to use it, (3) rapid experimentation, (4) support across the supply chain and (5) patience.