3-D Printing: Curbing Carbon One Part at a Time
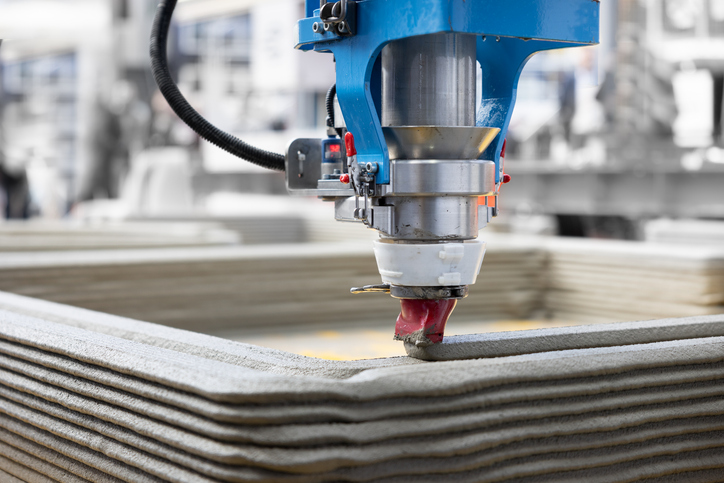
With a rise in global consciousness as well as the environmental, social and governance (ESG) standards, the apparel and textile sector is working to optimize profits and regulatory compliance. The sentiments and solutions differ, depending on the company’s country of origin.
As more companies get involved in reshoring, technologies like 3-D printing (or additive manufacturing) can reduce costs and waste, increase efficiency, and ultimately provide consumers more product choice in less time.
Cleaner Output by Design
Research has shed light on the harms to ecosystems from apparel and textile industries. Environmental advocates and scientists consider both textile and garment processing supply chains the biggest sources of airborne waste, with global transport releasing it into the atmosphere.
For years, standard practices included procurement of carbon-heavy materials and fabrics to minimize operating costs and keep manufacturing plants afloat.
The United Nations (U.N.) Environment and Development Programme UNEA 5.2 resolution and U.N. Sustainable Development Goals (SDGs) propose action through stronger global sustainability development plans, but more can be done, says Fabian Alefeld, senior manager of additive minds at manufacturing innovator EOS.
“There’s a lot of innovative manufacturing technologies out there that aren’t leveraged today. Technologies like additive manufacturing allow companies to innovate their supply chains and their manufacturing, and greater sustainability is a beneficial byproduct,” he says.
The Cost of Antiquity
Comparing Europe to the U.S., Alefeld says there are differences in what’s moving sustainability initiatives. For the U.S., he suggests that cost, profitability and opportunity are the primary drivers, yet additive-based manufacturing provides those qualities as well as sustainability.
“If we look at how the apparel industry works, there are parallels. For example, the eyewear industry,” he says. “Some people call it a medical device, while others a fashion item. The eyewear industry is not that sustainable or agile. For every piece of eyewear sold, 11 end up in a landfill.” For manufacturers, eyewear demand forecasting is nearsighted at best.
Unpredictability in consumer preference affects entire supply chains, Alefeld says, creating production and stockpiling issues. Once a company launches a new product line, the “warehouse must be fully stocked to meet that demand,” he says. “But if 10 new designs are launched with only five hitting demand, now the warehouses sit idle with product.” Special promotions and deep discounts can help, but it’s seldom enough, he says.
Eyewear design through 3-D printing is the opposite approach, a retrofit production process. “Product launches can include multiple designs, but you don’t have the stress of back-end stock. It’s an on-demand print platform allowing customers to design their eyewear,” states Alefeld.
The made-to-order collaborative business model includes user interface for the measurement and fine-tuning of product. “Through an app, users scan their face into an iPhone and receive digital eyewear frames that can be adjusted for a better fit. Within a couple of weeks, the prescriptive eyewear is delivered,” he says.
Manufacturing Freedoms
Additive manufacturing presents many values across manufacturing supply chains. For Alefeld, it removes complexities while augmenting them. “We can manufacture on a local level, reducing supply chain complexity,” he says. “3-D printing of parts gives us design freedom allowing companies to produce parts that are lighter, yet more complex. You see this in the space industry — a lot of the thrust chambers are 3-D printed enabling higher performance, impossible to duplicate in conventional manufacturing.”
EOS has conducted additive manufacturing cost and carbon footprint analyses, he says, running a full life-cycle assessment of eyewear, comparing 3-D printing to machine output, using acetone. The study, a collaborative with the Fraunhofer Institute, Alefeld states, resulted in a 45-to-55 percent reduction in carbon dioxide (CO2) equivalent, including production.
Retooling Procurement, Better Output
Large manufacturers can innovate faster and launch smaller product lines more expediently changing procurement tooling. Alefeld cites injection molding tools that can be printed including complex or conformal cooling channels, which improve and increase outputs by 40 percent.
For businesses wanting to test a market before committing to full production, direct print of one part of a product or line is the solution. If the response is good, “we can flip the switch to a more conventional and larger manufacturing technology,” he says.
Smaller companies will also find benefits in additive manufacturing, as it allows them to bypass the large manufacturing cells in the Asia-Pacific region that typically require huge capital investments or a minimum order (quantity) contract. Instead, these boutique businesses can produce only the parts needed, he adds.
Diversity: From Product to People
If you look at the apparel market over the last 20 years, “everyone wore the same brand, the same pair of jeans, whatever was cool in the moment, and there wasn’t much diversity,” says Alefeld. But thanks in big part to social media, people dress more individualistically than before, he notes, crediting the manufacturing industry’s ability to meet those diverse tastes.
“Shifting into digital supply chain management and digital manufacturing technologies like 3-D printing will help the big guys and the smaller manufacturers,” he says, providing equitable opportunities and increasing sustainability and innovative practices across the board.