The Monthly Metric: Total Recordable Incident Rate
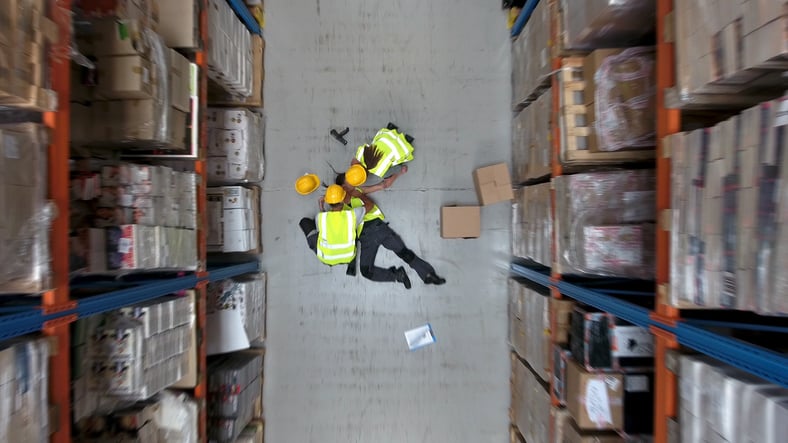
Although analytics that measure performance have not previously been a focus of The Monthly Metric, the issue of workplace safety is a significant one for supply chains — which is quickly confirmed by a glance at recent headlines.
While incidents at warehouses or construction sites garner much of the news focus, workplaces of all locations and sizes can face severe consequences — legal, reputational and financial — for safety violations. Under the Occupational Safety and Health Act of 1970, workplaces with 10 or more employees are required to keep illness and injury records under guidelines set by the Occupational Safety and Health Administration (OSHA), and agency of the U.S. Department of Labor.
As a result, one of the most important metrics for a company is its total recordable incident rate (TRIR), also known as total case incident rate or OSHA incident rate. Since OHSA uses the metric to gauge workplace safety risks in companies and industries, a high TRIR can put a company under risk of fines and other penalties. There are also potential insurance and employee recruitment ramifications.
Workplace safety and incident rates are often-discussed topics among the human resources (HR) community, says Trina DeWitt, HR Director at Institute for Supply Management® (ISM®). She has worked in the consumer electronics retail industry, “where risk of injury was high in the warehouses and distribution centers,” she says.
In a traditional workplace, injuries aren’t the main safety focus; it’s more about ergonomics, DeWitt says. “But you still must be on top of reporting and training when needed,” she says, adding that compliance and reporting dynamics apply to on-site and remote employees.
Meaning of the Metric
TRIR is calculated by taking a company’s number of recorded injuries in a year and multiplying it by 200,000. That figure is then divided by the number of hours worked in a year. According to OSHA, “the 200,000 figure in the formula represents the number of hours 100 employees working 40 hours per week, 50 weeks per year would work, and provides the standard base for calculating incidence rate for an entire year.”
The scenarios in which a work-related incident must be reported, OHSA requirements state, include if it (1) is fatal, (2) results in loss of consciousness, missed days, restricted work or transfer to another job, (3) requires treatment beyond what a first aid kit can address, (4) results in fractured bones and/or teeth and punctured eardrums or (5) leads to a diagnosis of cancer or another chronic, irreversible disease.
There have been concerns that TRIR rates can be manipulated by companies self-determining a reportable incident or simply not reporting an incident, even though that risks a US$5,000 fine. Also, many workers injured on the job don’t alert employers: “Folks fear retaliation (or) don’t recognize their injury as being caused by work,” Marissa Baker, Ph.D., an associate professor in the environmental and occupational health sciences department at the University of Washington in Seattle, told Marketplace.
Incident Rates Across Industries
However, the most reliable industry benchmarks remain the employer-reported workplace injuries and illnesses data reported by the U.S. Bureau of Labor Statistics; these figures do not include fatalities.
In 2022, the average TRIR for U.S. private-sector workplaces was 2.7 cases per 100 full-time employees (FTEs). Among industries, the highest was transportation and warehousing (4.8), followed by health care and social assistance (4.5), arts, entertainment and recreation (4.2) and agriculture, forestry, fishing and hunting (4.1).
Among the most reported incidents: overexertion and bodily reaction, harmful contact with objects and equipment, exposure to harmful substances and — in a world where COVID-19 remains a threat — respiratory ailments, particularly in the health-care sector. About 365,000 workplace respiratory illnesses were reported in 2022, up from 10,800 in 2019.
The total of 2.8 million nonfatal incidents was an increase of 7.5 percent compared to 2021. The work-related fatality rate was 3.7 per 100,000 FTEs, up from 3.6 the previous year.
While the incident increases are due in part to many employees returning on-site, companies are liable for employees that work remotely, DeWitt says. “If someone is having back issues or some other pain because their home office is not ergonomically designed, a company is obligated to help with that,” she says. “It could be a matter of (the employee) taking a photo of his or her work station, so assessments and recommendations can be made.”
Safety Issues Have Consequences
In a rule that took effect on January 1, OSHA gave companies and incentive to improve TRIR. The rule expands workplace incident submission requirements, and companies’ data will be subject to publishing on OSHA’s website.
“OSHA will use these data to intervene through strategic outreach and enforcement to reduce worker injuries and illnesses in high-hazard industries,” Doug Parker, U.S. assistant secretary of labor for occupational safety and health, said in a press release. “The safety and health community will benefit from the insights this information will provide at the industry level, while workers and employers will be able to make more informed decisions about their workplace’s safety and health.”
Such public disclosure intensifies potential consequences for high TRIR that include:
- On-site inspections by OSHA and/or state regulators, raising exposure for fines and penalties like stop-work orders that can impact project timelines and budgets
- Raised insurance rates and premiums
- Prospective employees, contractors and suppliers that are hesitant to work for or with a company that has safety issues.
For a company that taps resources to improve workplace safety culture and incident prevention, significant progress is possible. DeWitt recalls a consumer electronics distribution center with a history of safety issues: “The leadership changed, and it worked with OSHA on follow-up inspections and training,” she says.
“When 100 days passed without an incident, the company brought in food and everyone had a couple of hours to eat and celebrate. After the problems the facility had, that achievement deserved to be recognized.”
To suggest a metric to be covered, email me at dzeiger@ismworld.org.