Ocean Shipping Disruptions Emphasize Criticality of Data
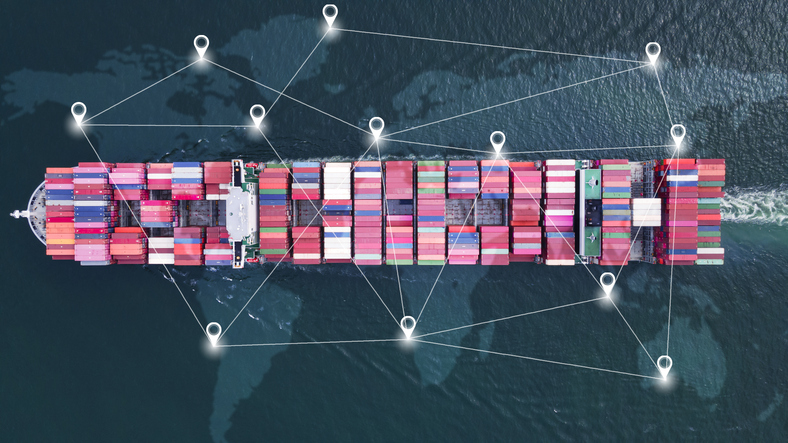
Customers and consumers are driving the show for supply management organizations when it comes to managing the shipping crises occurring in the Red Sea area and the Panama Canal.
The omnichannel environment of today mandates “any place, any time.” But these shipping crises are disrupting the ability to meet end-user demands and needs, causing delayed shipments and higher costs that translate to increased prices.
Shipping rates, for containers as well as air cargo, have risen. Ships have diverted to new routes.
Changing shipping processes, lanes or even mediums during a crisis isn’t easy, nor is reverting back once a disruption has ended, says Melanie Nuce-Hilton, senior vice president, innovation and partnerships at GS1, a nonprofit international organization that develops and maintains its own standards for barcodes. But technology — from RFID to artificial intelligence (AI) — can aid in facilitating the process as well as anticipating what’s next.
Not only prevalent in retail, omnichannel has slipped into all aspects of supply chains, as organizations want quick lead times, delivery times and the most efficient shipping methods and routes.
Therefore, it’s imperative, Nuce-Hilton says, that supply management organizations have visibility into their supply chains as well as the right data to make the most informed decisions on shipping routes, product transfers, sources of supply and the like.
Data Can Aid in Crisis Management
The coronavirus pandemic raised the awareness around the notion of supply chain resilience — the ability to survive as well as thrive in the face of adversity. One of the biggest contributors to a lack of resilience is a lack of visibility, Nuce-Hilton says.
“It’s not so much about ‘I can’t find my container,’ ” she says. “I know where the container is. It’s (visibility into) all the factors around it that are creating that disruption.”
Consider barcode technology. “Think of barcodes on pallets on containers that are going different places in the supply chain,” she says. “Reading that barcode and having a link back to the data of what’s in that palette and what’s in that container can be really helpful in terms of informing your mitigation strategy.”
Another technology enabler: AI. It can look at a variety of data sources and make recommendations around different business decisions, she says.
“Machine learning and AI can become an equalizer because if you can get access to the data, you can put the data to work for you,” Nuce-Hilton says. “A human can only compute so much.” While computers can’t sense all of the nuances, they can “take a bunch of data and churn out some ideas,” she says.
Even so, humans aren’t lost in the process. “There is a lot of talk in AI around the human in the loop, the person who (1) validates what the AI is saying and (2) directs the ask. “If you ask AI for three scenarios, you get three scenarios. The human in the loop is the one who decides which scenario makes the most sense because the human has had other conversations around the situation and (may know) pieces of data that weren’t available to the computer.
“It’s kind of an exponential decision-making capability when you take human decision-making and AI and pair them together.”
Organizations used to look to data for trends and for expectations based on what’s happened in the past. Now, the focus is on prescriptive AI — anticipating the trends and disruptions. However, she says, there’s still a need to:
- Ensure that the data being collected and analyzed is clean, complete and consistent
- Facilitate data sharing with partners to drive profitability for all parties. This can be a difficult concept for some organizations to embrace because it’s not the way things have been done in the past, she says.
Putting Lessons Learned to Use
While data and technology can be game changers for management of current and future disruption, lessons learned from past events — like the pandemic — also can be useful. Have supply management organizations incorporated these lessons learned during the Red Sea shipping crisis?
“I feel it’s a different set of lessons,” Nuce-Hilton says of the current crisis. “There will always be something more to learn.” Still, the pandemic did advance supply chain technology, she says: “I heard one grocery CEO say we have now leapfrogged five years of technology into two to three months. So, the pandemic taught that.”
But for organizations, operational budgets are a reality and “the bottom line is still the bottom line,” she says. “They can only flex that so much at any given time. So, the challenge is we can't predict what the next crisis will entail. That’s maybe what keeps us on our toes — that we can learn from the event that happened but until the next unknown thing happens, it's very hard to predict what that is.”
Perhaps that’s where eventually the massive amounts of data being moved through AI will start to pay dividends, Nuce-Hilton says. The data will show patterns or the potential for actions, with varying degrees of confidence.
“Believing in the data is really critical for us to anticipate the next thing,” she says. “Maybe what we’ve learned is that data can be our ally if we put it to work properly, and that it’s always best to try to work on it when we’re not in crisis mode.”