The Monthly Metric: Fulfillment Cost Per Order
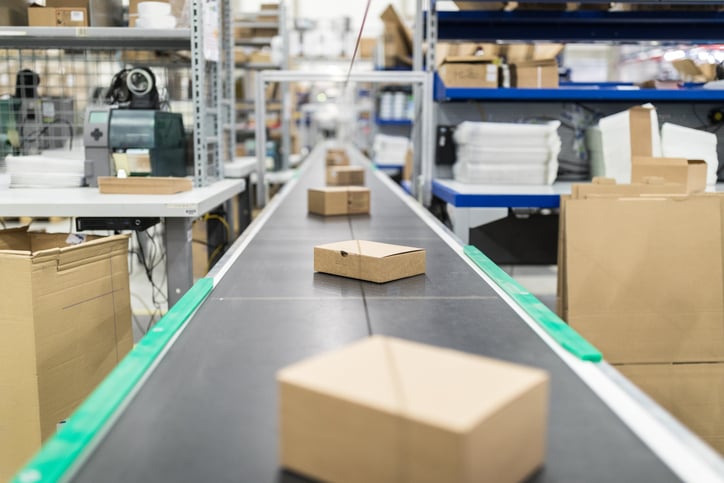
With warehouse rents continuing to rise around the globe, the expense of simply storing a product or supply is taking an increasingly bigger bite out of order fulfillment cost.
Rent can be a pain for companies trying to contain this month’s metric, fulfillment cost per order, but it might not be the highest-profile headache: Logistics is hardly the only industry in which labor costs have risen. Calculating fulfillment cost per order goes far beyond facility and employment expenses, and other critical elements can be overlooked.
That makes fulfilment cost per order a challenging analytic to measure, says Brian Barry, president at F. Curtis Barry & Company, a Richmond, Virginia-based warehouse operations and fulfillment consultancy. But, he adds, accurate tracking of the metric, also known as warehouse cost per order, can bring value beyond a storage facility by helping companies find breakdowns in their logistics operations.
“(The metric) can identify trends before something gets out of control,” Barry says. “It can help you find areas that are struggling. If your cost per order going up month over month, you want to understand why.
“If I’m shipping more lines and units on an order, that could drive up cost. But if my lines and units are more or less flat, something is happening. Do I have congestion that’s causing more time to pick and satisfy an order? Knowing what’s causing the trend — why your cost per order is rising — will help you resolve those bottlenecks.”
Meaning of the Metric
As the name of the metric indicates, fulfillment cost per order can be calculated with a simple fraction, total warehouse cost divided by orders shipped over a fixed time period; Barry recommends at least quarterly measurements, though monthly is most ideal.
Determining and collecting the data to calculate total cost is more complex and requires help from multiple functions. What Barry describes as a “fully loaded” fulfillment cost per order should include all relevant operational expenses, including:
- Labor costs associated with order fulfillment: receiving, inspection, putaway, picking, packing, shipping, returns, inventory control and the like
- Management and supervisory labor directly associated with operations, such as clerical, transportation, janitorial and security
- Facility costs: mortgage/lease, taxes, insurance, utilities and maintenance, with depreciation and amortization for warehouse equipment and systems factored
- Packing and shipping supplies
- Reverse logistics or returns processing.
“Silos of data can complicate things,” Barry says. “A company will have a lot of warehouse and shipment transactional data and must get help from accounting, especially for payroll and benefits data and the facility costs. With all of these different cost buckets, it’s a challenge sometimes to streamline the data.”
The key, he says, is consistency, getting stakeholders to agree on how the metric is calculated and which data is used. Then, be consistent in measuring it.
An expense to not include in the calculation — shipping and handling. Barry says that freight costs and other dynamics that caused logistics turmoil during the coronavirus pandemic can create wild cost per order swings that “unfairly burden the calculation,” he says. Supply managers should always strive for the best shipping and handling value, Barry adds, but the expenses should be tracked separately.
“There’s debate around this, but we’ve taken the approach that shipping and handling costs are not part of this metric,” he says.
The Best Benchmark is Your Own
Some firms, including F. Curtis Barry & Company, have published benchmarks for fulfillment cost per order, but companies have different dynamics — including product type, level of automation, labor costs and customer base (B2B or e-commerce) — that make comparisons less useful. A company’s most insightful benchmarking, Barry says, is against itself.
A year of data should provide a good picture of a company’s fulfillment cost per order performance during seasonal peaks and valleys, as well as potentially reveal operational areas that require deeper analysis. A company can get even more granular and calculate fulfillment cost per order line, per box shipped and as a percentage of net sales, Barry says.
“Benchmarking data can be muddy if you don’t know what’s behind another company’s numbers from a white paper,” he says. “Our firm’s audience is mostly e-commerce, and that’s a different animal than B2B or wholesale distribution. This is one of those metrics where it’s better to be consistent and measure yourself over time.”
How to Improve Performance
While fulfillment cost per order is an aggregation of expenses, it’s critical to keep the data granular enough that issues can be easily identified, Barry says: “You don’t want just one big bucket of costs. You want facility costs separated from labor, for example.”
He continues, “It’s important to keep those buckets separated, so that if you see cost going up, you can drill down into it. If packaging costs have gone up, it could be because you have started shipping a fragile product. What are your alternative packaging options?”
Outdated warehouse technologies or space inefficiencies can slow labor and result in unnecessary multiple shipments. Examining such analytics as dock-to-stock cycle time can lead to process improvements and lower costs.
Tracking fulfillment cost per order can’t address elevated facility rent, but there are other cost buckets in which the data can unlock not only costs savings, but smoother supply chain operations.
“A company may be in a five-year lease for a facility, so a supply manager has no ability to change that cost over the life of a contract,” Barry says. “But how a building is used from a capacity and utilization perspective and how labor is managed will impact (fulfillment cost per order). You should always be on the lookout for things to tweak to for your warehouse to be as efficient as possible in all areas, and this metric can help.”
To suggest a metric to be covered, email me at dzeiger@ismworld.org.