How Tech Layoffs Spur Supply Chain Innovation
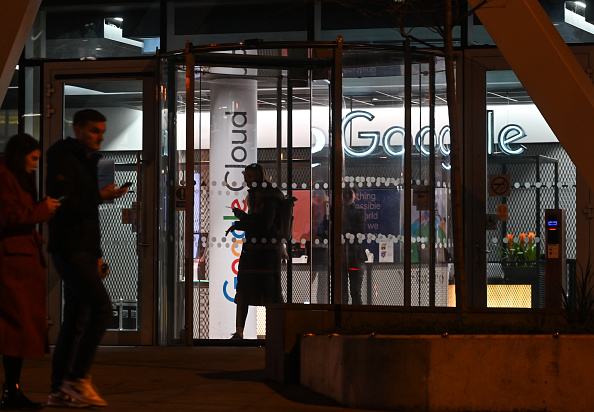
Evolution spurs revolution, evident in supply chain disruptions and the impact they generate. The Fourth Industrial Revolution was already born when COVID-19 and other challenges changed the way business approached growth, risk and survival.
Technology is the tacit facilitator, with the people behind it in demand — including supply management organizations, which could impact the makeup of workforces, says Matt Spooner of Canadian supply chain management software company Kinaxis. “Many seasoned practitioners came into the profession from other industries, education and experiences,” he says. But it made supply management an incredibly diverse community with an abundance of abilities, he says.
While the current talent pool has similar backgrounds, degrees and specialty focuses such as data science, mathematics and engineering, Spooner has concerns that the new talent may create one-dimensional perspectives within the profession. This, he says, “could compromise our ability to create innovative solutions.” When people with backgrounds in finance, operations, marketing and sales entered the supply management workforce, they brought additional clarity for envisioning the impact of initiatives, spend, reorganization and more, a distinct benefit, he says.
Technology Is the Bellwether for Hiring
Recent downturns in the technology sector have forced some companies to reduce head counts, propose early retirement offerings and initiate layoffs of highly skilled employees. Spooner sees this is an incredible opportunity for supply management.
“We have a massive shortage of talent within the profession because tech companies, like Google, have been very attractive to top talent for some time. But the dynamic of the labor market is changing and caution is creeping in,” Spooner says. With the recent tech layoffs, supply chains can build upon the push to recruit emerging and seasoned professionals, he says, to better position for the increased technology and artificial intelligence (AI) use to come.
Investing in digital technologies, machine learning, AI and people ostensibly presents huge opportunities and aligns with the kind of talent supply chains seek, he says. Hiring, like other spend categories, should not be postponed but exercised, especially in times of ongoing disruption, adds Spooner. “It’s an investment, and we need to change the way we look at it,” he says.
Prioritizing Digitization’s ROI
Spooner is adept at identifying areas of business practices that can be enhanced through a shift in ideology. He views disruption as the means for an organization to gain market share from competitors. “By investing in technologies and better product innovation, you can enhance sales and marketing,” he says.
Disruptive times are not the time to pull back, he notes, adding it’s the time to do more to reach your customers. The standard expectation for a digital technology ROI is three years, but Spooner says amid volatility, companies should be looking for a faster return.
“A nine-month ROI is entirely possible, especially with consumer goods companies,” he says. Instead of creating a highly customizable solution, Spooner suggests using a best-in-class, out-of-the-box solution. “There’s no need to reinvent the wheel,” he says. “Out-of-the-box options can provide a faster pay back than what you have now.”
Controlled Agility and the Cost of Resiliency
Conversations among practitioners extol references on having a better ability to manage the supply chain. Spooner cites it as pretense: “We’re just more familiar with disruption and we expect it. The supply chain remains as complex as it’s ever been.” But there is a contradiction to agility and its anticipated outcomes, he says: “If you are too agile — trying to react to every single disruption or change — you can create instability through the agility, increasing uncertainty and with it, potentially, additional costs.”
A more sensible alternative to agility and hyper-agility, he says, is to exercise “controlled agility,” applying deeper consideration and assessment of each challenge and the type of response warranted.
Finding an effective balance in technology spend can lead to greater resiliency, as long as decision makers understand that the potential revenue to be gained will far outweigh the cost, Spooner says. “Typically, supply chains focus on minimizing operating costs, scrutinizing every dollar,” he says. “If you don’t have the technological infrastructure in place to help mitigate the disruptions to come, that adversely affects resiliency and adds costs.”
A 2022 McKinsey & Company survey showed that two-thirds of respondent companies indicated disruptions adversely impacted their revenue between 5 to 10 percent, Spooner says. “There are costs to building resilient supply chains, but the costs to an organization are far greater without resiliency,” he says, adding that having the right talent can be the glue merging technology and its optimal application.
Beyond Data Science
Among current supply chains, Spooner says, “98 percent of them illustrate weakness in Tiers 3 and 4 in how they work with suppliers to resolve challenges.” He believes that tech talent can lead initiatives to generate greater visibility and collaboration across all tiers.
“The talent we need goes beyond data science expertise. It’s having people who really understand how to manage supply chains and apply the data science properly to gauge decision-making today and tomorrow,” he says. Employment candidates and active workers have dynamically shifted their mindset. Spooner sees former job roles modeled in ‘silo’ tasks moving toward collaborative efforts with an eye on the bigger picture.
“Everything we’ve learned in the last 30 years,” he states, “needs to be unlearned to address our future needs. The professional capabilities required for the next five years are going to look very different.”
The Abyss of Sustainability
Depending on where you do business in the world, the tenets of environmental, social and governance (ESG) regulations come with varying degrees of acceptance and adoption. “It’s talked about at the board level, but the investments aren’t matching the talk just yet,” Spooner says.
With the rulings in place governing financial reporting and misreporting, he says ESG reporting should be practiced and penalized in the same manner. “With legislation, it creates a level playing field,” he says. “Sustainability should be a priority, from manufacturing to distribution and consumer use of those products.” Therein lies a disconnect.
“Our economic model is based on consumption. The global pandemic altered consumer behavior, generating more ‘waste.’ Now people replace goods more and more frequently,” he says. For example, clothing, on average, is worn less than 10 times before replacement. Spooner says this is a social and ethical issue that the fashion industry can take on and formulate a win.
“Let’s incorporate the repair, reuse and rework of products and solutions through supply chains to repurpose these items. This is more than ESG; our supply chain models can evolve to better support sustainability,” he says.
Forward Thinking
The profession is growing and attracting more talent, with supply management graduates experiencing some of the highest rates of employment.
Spooner says the education-to-hiring trend will naturally spill over into other areas of business, including technology and sustainability, likely leading to more interest and opportunities in supply chains.