How Data Truth Keeps Food Safe and Companies Compliant
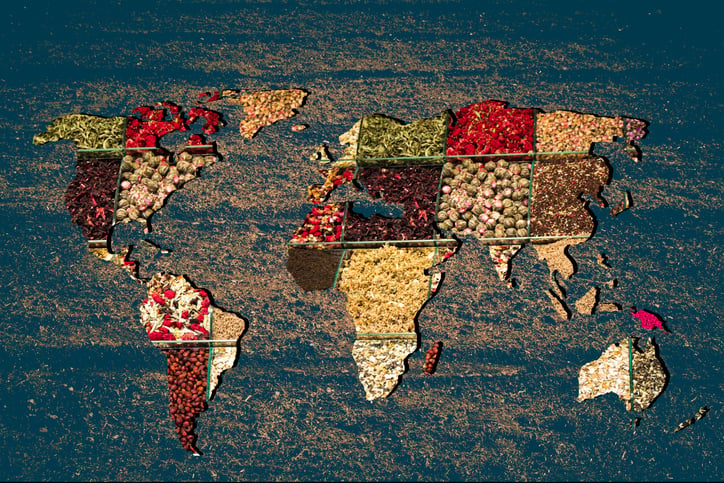
Businesses and consumers put a lot of faith into the global food supply, as its sourcing, certifications and labeling put a stamp on integrity, reliability and safety.
Recent years have shown that regulatory agencies and the governments behind them can issue pause on protocols when unforeseen circumstances strain food supplies and demand overshadows the risks in utilizing alternative or unverified sources.
Under the American Disabilities Act (ADA), non-allergen-based foods businesses are a protected class. The U.S. Food and Drug Administration (FDA) allows food and beverage companies to avert label changeswhen using alternative ingredients in product, though the same does not apply to foods with non-allergen applications.
Finding data truth in labeling and certification lies in the accessing and updating of information, says Lucas Cunha of New York-based Otrafy. “Enabling and utilizing data truth leads to food safety, quality and compliance problem-solving,” states the chief operating officer and co-founder of the AI-powered supplier compliance and risk management software company.
Behind the Looking Glass
Visibility and greater transparency are essential for food suppliers and their customers, says Cunha. It is an imperative, more evident with specialty businesses who require certifications, such as kosher or allergen-free products that carry more regulation and risk. “Data technology helps decision-makers stay compliant in a time-efficient way,” he says. However, if a business continues to use antiquated ways of creating and compiling data, human error increases risks across the supply chain.
“Companies have a hard time collecting and maintaining data, as it mostly rests on (Microsoft) Excel spreadsheets, Word documents and Post-it notes kept in unshared files or inaccessible emails,” he states. People tasked with this type of work often change jobs, he says, “leaving companies with a messy situation. Imagine waiting on an approval of a product or ingredient, but the details about it are sitting in a locked email.” He says assumptions could be made either way, and if acted upon, add risk.
Data is only as good as its accessibility and accuracy, Cunha says: “If you don’t have that, understanding where your sourcing was compared to where it is today is near impossible.” Many companies don’t have visibility inside their own walls, he says, but integrating a single-source, internal information solution, data sourcing and verification problems can alleviate problems.
Bringing Food Processes Up to Date
Developing visibility and transparency into the food supply chain can be complex; ingredients may need to be sourced from multiple countries, each with diverse customs and cultural idiosyncrasies — and regulations, Cunha says.
Documents and processes associated with compliance reporting and certification verifications are compiled from the data provided by buyers and sellers. “This could range from allergen questionnaires, third-party audits, and clean label certificates like kosher, halal, organic, non-GMO (genetically modified organism) and more,” he says. Without a single-sourced system in place, data inaccuracies, inconsistent updates and language barriers challenge food safety, quality assurance and compliance.
Data Truth Is Risk Mitigation
Having greater end-to-end transparency is especially important for specialty foods customers. The ability to make claims on products, through halal and kosher religious certifications or when working with allergen-free companies, is the basis of their credibility.
“When a food safety event happens, brand reputation will be damaged,” Cunha says. “For public companies, it will affect share price as well. Once customers lose trust, it’s hard to get it back.” When companies rush the production process leaving little time to check on quality, risk rises, he says.
“Imagine what would happen if a batch of an allergen-free product was exposed to peanuts during the manufacturing process, eventually reaching consumers,” he states. In addition to the allergy attacks and potential life or death scenarios, there are recalls, negative press and the impact to the brand that will take some time to restore, if ever, he says. Many companies don’t consider these kinds of risks until an event happens. “Having access to data is crucial to quality control and risk mitigation. Without it, the repercussions will fall completely on your shoulders,” he says.
Trust But Verify in Real Time
For food manufacturers and suppliers carrying a kosher or halal designation, collecting and securing the information verifying certification defines their success or failure.
Before data technology, the procurement of religious-certified ingredients was tedious and time-consuming — and often difficult to procure, Cunha says. The process would begin with an email listing 40 ingredients from five facilities, for example, specifying areas of importance that must be met, he says. But the supplier might be able to provide only 10 of the 40 ingredients from two of the five facilities, leaving 30 missing ingredients, he says.
Verifying the ingredients can be equally difficult. The email list serves as an ingredient sourcing document, Cunha says; it is reviewed by a highly specialized, Ph.D.-trained, food-safety scientist with green and yellow markers in hand, checking which ingredients pass certification. Should an auditor question an ingredient or food product and if the data verification document does not match the certification claim, it will be costly as well as time-consuming to manually search through Excel spreadsheets, emails or Post-it notes to find answers, he says.
By integrating food safety data AI, customers receive sourcing verifications much quicker. “Companies can look at the data verification and find food certification matches in real time. Or they can source kosher- or halal-certified products, simply by asking the platform and it will be provided,” Cunha says. Such a program also allows buyers to accept, reject or request changes directly with suppliers more accurately and expediently, he says.
A Collaborative Resource
In recent years, disruption to food supply chains escalated the need for sourcing alternative suppliers to keep production, distribution and sales moving. Cunha says that before 2020, typical quality assurance practices entailed document review for what was required at that moment in time.
“Now, through AI, businesses have access to sourcing alternatives before the need arises, thus saving time and mitigating further disruption,” he says. Data verification capabilities go beyond identifying the right sources to meet with certification compliance, he states: “It’s about doing the predictive work to better support supply management and the consumer experience.”
Single-source data AI supports a more efficient and transparent supply-chain system, Cunha says: “For partners or auditors, they want people to follow the right practices. For buyers, they need efficient data access through automation. Suppliers just want to sell product without the hiccup of documentation verification potentially putting a hold on an order.”
With more data and greater accessibility, he says, food supply and procurement can execute more visible transactions, while transparency keeps it kosher.