Greater Supplier Network Resiliency Through Digitalization
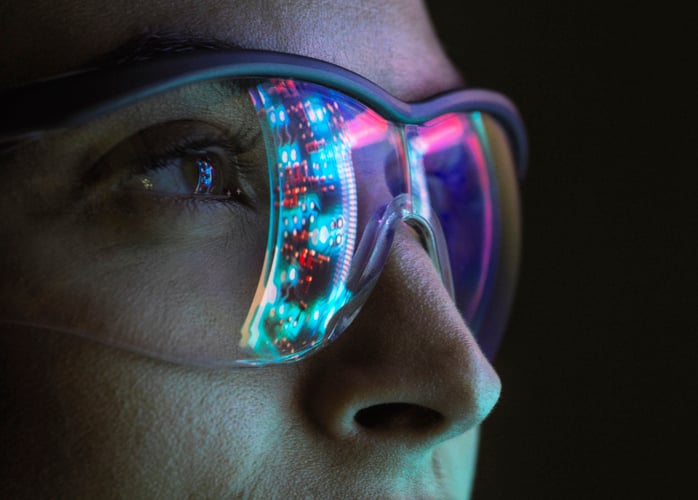
Businesses have long understood the risks of being overly dependent on a single country for production, but only in recent years have they experienced the consequences. The coronavirus pandemic and the trade war between the U.S. and China severely strained supply chains, leading to raw material and component shortages, price surges and enormous port backups.
Now, supply chain leaders who had previously been slow to implement measures to geographically diversify their supplier base are recognizing the need for change.
Last year, BCI Global forecasted that more than 60 percent of U.S. and European manufacturing companies plan to relocate some of their Asian production over the next several years. That’s likely to translate into more business with India and Vietnam, countries that many U.S. companies say they see as attractive alternatives to Chinese manufacturing.
It could also mean more nearshoring, a practice that would help companies meet their long-term sustainability targets. With shorter shipping distances reducing the environmental footprint of products, and by moving production to countries with tighter labor regulations, companies could also alleviate concerns about forced labor in the supply chain. Some U.S. companies have already started relocating production to Mexico as competitive wages, lower transport costs and environmental benefits have made sourcing from that country more attractive.
As organizations work to build more resilient supplier networks in response to economic and political volatility, they must start by investing in digitalization. Once seen as a competitive advantage, supply chain digitalization has become an indisputable necessity as the supply chain has grown more complex and more outsourced.
Digitalization Advances
Supply management organizations have made some recent progress toward digitalization. Nearly 78 percent of supply chain leaders reported accelerating their digital transformations in the wake of the pandemic, and those investments should help them better navigate the obstacles that lie ahead.
However, some of the systems they’ve implemented are too narrow and don’t integrate as frictionlessly as needed. This results in complicated, patchwork systems of sometimes incompatible software and creates inefficiencies that counteract the very benefits that encouraged companies to digitalize in the first place.
Businesses that outsource their supply chains need to optimize their processes from end to end to ensure their systems are compatible. That means implementing a multi-enterprise platform that can streamline everything from sourcing, logistics and product development to supplier, order and quality management, all of which are integral for controlling costs and helping businesses mitigate supply chain risks.
A multienterprise platform helps businesses more quickly identify, select and onboard suppliers, allowing companies to diversify their supply chains faster. It also facilitates smarter, more cost-effective material procurement. The right system can not only identify missed cost-savings opportunities and show landing costs for different commodities based on countries of origin, but also help predict demand and identify alternate or future supply sources.
Digitalization creates visibility into prices, supply bases and costs, enabling predictive sourcing and allowing buyers to negotiate more transparent agreements. When brands and retailers have visibility into previously unused sources and suppliers, they’re better able to mix and match materials during the specification and procurement process. This visibility is key to sourcing competitively, especially for businesses that are geographically diversifying their supplier bases or branching out into new product categories.
Staying Ahead of Due Diligence Laws
For compliance teams and supply chain sustainability managers, the benefits of digitalization with a multienterprise platform are especially profound.
Due to recent regulations like the U.S.’s Uyghur Forced Labor Protection Act (UFLPA) and Germany’s Supply Chain Due Diligence law, large brands and retailers face more stringent requirements. To meet them, they need complete documentation of all suppliers, from raw materials to finished goods. They also need to document the full chain of custody of materials, such as where they were shipped from and where they were made, including all transformations from raw materials to finished goods.
In the wake of heightened environmental, social and governance (ESG) standards, there has been more interest in supply chain mapping and chain of custody management, which help safeguard against lengthy detainments and possibly heavy fines while enabling businesses to source to higher standards of responsibility. Such platforms also enable businesses to more accurately back up the sustainability claims they make about their products — which is essential, as regulations have pushed back against greenwashing.
The UFLPA has already caused some organizations to cut back on sourcing from China, especially imports like apparel, polysilicon and polyvinyl chloride, which are among those most at risk of containing forced labor.
But reshoring alone isn’t enough to ensure compliance with the law or to guarantee no forced labor was involved in a product’s supply chain. For that, businesses need the visibility into a company’s supplier base a multienterprise platform provides. Amid the growing complexity of the supply chain, this transparency is critically necessary for brands to make the most responsible and strategic procurement decisions.