Inside Supply Management Magazine
Managing the Coronavirus Outbreak’s Supply Chain Impact
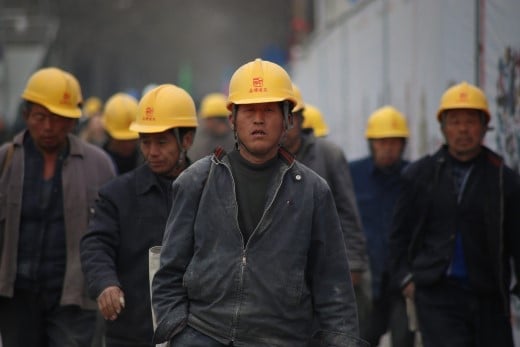
The ramifications of the coronavirus outbreak on supply chains could last months, a Gartner expert says. And the longer the outbreak is prolonged, the greater the impact, says Koray Köse, senior director analyst at the Stamford, Connecticut-based global business research and advisory firm’s supply chain sourcing and procurement team. He is the lead author of Gartner’s recent Global Supply Chains Prepare for Impact From Coronavirus report.
Dwindling inventories, decreased exports from China and the need to find alternative sources are just some of the disruptions supply chains face — but until now, the impact has been minimal, Köse says. It will become more apparent as Chinese factory workers return to their jobs this week after the extended Chinese New Year break.
“The coronavirus outbreak coincided with Chinese New Year, and that’s good and bad,” he says. “It’s good because companies are always prepared for the Chinese New Year disruption — therefore, we haven’t seen much of an impact to the consumer yet.” But alternatively, as workers return, the virus is only likely to spread further, creating greater impact to companies and their customers, he says.
Mitigating Risk
Short- to long-term recommendations, detailed in the report, can help organizations mitigate the impact.
Short term. “If you haven’t already, make sure you understand your full exposure before you act,” Köse says. Organizations must assemble a cross-functional crisis-management team with stakeholders from such areas as engineering, manufacturing, procurement, supply chain and logistics, and assess the situation, he says. “Work with your suppliers and demand team to determine how you are impacted and where your supply is coming from, including second-tier and lower-tier suppliers,” Köse says. “Then, move and build up inventory outside of the impacted area — but within the reach for your manufacturing and utilization. Do that now.”
Mid-term. In the next 30 days to three months, as the crisis unfolds, continue the short-term strategy while analyzing other factors affecting business continuity and mitigating them. “It’s a dynamic process,” Köse says. “You also need to look into enhancing your supply chain resilience, your risk appetite and risk management framework … and diversifying your dependencies and resources."
Long term. Organizations need to execute on their mid-term plan while “building up a dynamic risk-management framework, in which you set up a risk management awareness and action plan relating to situations such as force majeure,” Köse says. It’s not just “response, recovery and restore” — it’s determining preventive actions, he says.
Most importantly, he notes, organizations should set up a risk-appetite statement that (1) aligns with their business strategy and (2) is cascaded into key risk indicators, which will help them measure their exposure.
Proactive Planning
For supply management organizations, the coronavirus crisis should be “a wake-up call” that they need to set up a dynamic risk-management plan to handle impacts to their supply chains from such events, Köse says.
Crises like the coronavirus outbreak are going to continue to happen, he notes: “Our research shows that 89 percent of companies had a significant risk event in the last five years, and only 11 percent of all companies have a functional risk-appetite statement.” And few have defined their risk appetite statements to the extent that they are broken down by functional abilities and day-to-day tasks — and the key risk indicators associated with those, he says.
“It’s hard to comprehend how performance-driven, cost-cutting measures have been prioritized so much that (planning for) events like the coronavirus or the Japanese tsunami of 2011 gets overlooked,” Köse says. Companies tend to forget the crisis-management journey — or that the crisis management belongs to dynamic risk management, he says. All too often, organizations have a reactive, “recover and restore” mentality.
Dynamic risk management can enable organizations prevent the same impacts to their supply chains from reoccurring when a significant event happens, he says. What’s more, they’ll be able meet the needs of their customers before the competition does.