Inside Supply Management Magazine
The Monthly Metric: Procurement Staffing
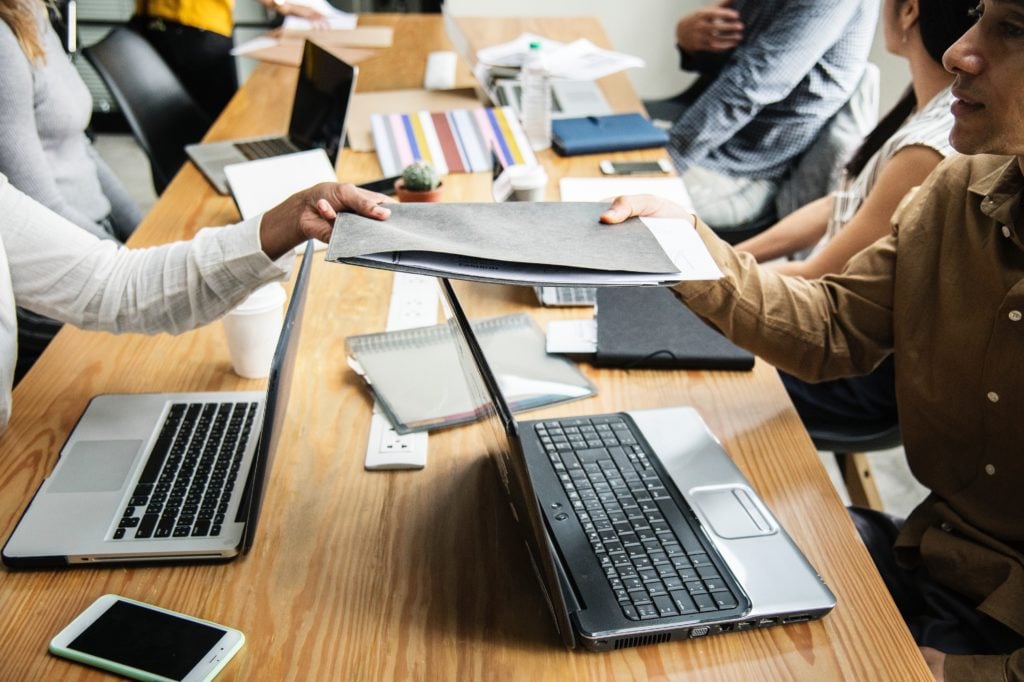
As has been mentioned regularly in The Monthly Metric this year, many procurement analytics are designed with one objective in mind — lowering procurement costs. A significant driver of those costs are labor expenses.
This month’s metric, procurement staffing, measures an organization’s effectiveness at deploying resources to deliver products and services to customers. However, a company that executes a supply management activity with seven employees compared to a similar organization that needs 10 has more than a productivity edge — its labor costs should be lower. And that makes staffing levels a critical measurement to track, says Chris Sawchuk, principal and global procurement advisory practice leader for The Hackett Group, a Miami-based business consultancy.
“When organizations ask how to continue to drive efficiency and ROI, you have to look at costs. One of the key drivers of organizational cost is the number of people you have performing supply management activities,” Sawchuk says. “If a certain number of people are conducting an activity and everyone else has fewer people doing the same thing in a similar environment, then a safe assumption is that you have a less-productive labor force. So, the question becomes what are those other organizations doing that you are not that allows them to outperform?”
What are more efficient companies likely doing? We’ll get to that later, but first, it’s important to discuss how procurement staffing is measured — and how some companies are likely doing it wrong.
Meaning of the Metric
The Hackett Group’s benchmarks measure procurement staffing by determining the number of full-time equivalents (FTEs) used to manage a common set of procurement activities per US$1 billion in spend. What The Hackett Group researchers classify as “world-class” companies have an average of 42.79 FTEs per $1 billion; that figure is 60.6 for other organizations.
Sawchuk says he has advised companies that initially think they are quite efficient; however, they account only for that report into a formal procurement organization (centralized or decentralized). FTEs are defined as employees who devote all or part of their jobs to sourcing activities, and they should factor into the measurement.
“Companies have people doing procurement activity who don’t report into the procurement organization and do not have a procurement title,” Sawchuk says. “HR staffers may decide on suppliers for HR benefits, and the sourcing organization might not be involved in it. This is sourcing activity, regardless of whether procurement is involved or not and needs to be accounted for. Procurement staffing needs to be viewed through an enterprise lens.”
If a non-procurement employee devotes a portion of time to sourcing activity, he or she is a partial FTE; for example, a worker in finance or manufacturing who places orders 40 percent of the time is a 0.4 FTE.
When determining peer organizations and setting benchmarks, Sawchuk says, it’s not as simple as comparing companies in similar industries. It’s also important to consider such areas as complexity, he says: “For example, you might have two organizations in the same industry with similar revenue, but one is a global company operating in 100 countries around the world and the other is a company operating in one country. Obviously, the complexity of these organizations is quite different and needs to be accounted for when considering comparisons.”
Rewards of Tapping Technology
According to Raising the World-Class Bar in Procurement Through Digital Transformation, a June 2018 report by The Hackett Group, “world-class” organizations have lowered procurement staffing figures primarily by standardizing and automating routine tasks.
“What we’ve found is that world-class organizations are leveraging several strategies,” Sawchuk says. “This includes such examples as activity elimination, process simplification, automation and service placement (for example, geographical and center of excellence). We have seen for many years a labor-for-technology swap occurring in the best-performing procurement organizations. Today, there are many new emerging digital technologies that are having an impact. Robotic process automation (RPA) is one and has the ability to take on repetitive tasks and impact the staffing needs of organizations. Most procurement organizations today are using RPA not to reduce staff, but to free up time and transition their staff to more strategic activities.”
The report states that, per $1 billion in spend, “world-class” organizations have slightly fewer sourcing and supply base management FTEs than typical companies. There is a more significant decline in FTEs for operations and compliance management in higher-performing companies, while there is little or no change in FTEs in management/administration and planning/strategy. The rewards: A 21-percent average lower procurement labor cost for “world-class” organizations, and a significantly higher procurement ROI (10.7, compared to 4.7 for typical companies).
“Technology has always played an important role in enabling world-class performance, but procurement is now at an inflection point: World-class organizations can continue to reduce costs by embracing digital technology, while the peer group can leverage the same technology to catch up faster at less cost,” the report states.
In an environment where supply management leaders are constantly challenged to do more with less, procurement staffing is a metric that can provide clarity on how to best mobilize employees and FTEs — and lead to cost savings.
To suggest a metric to be covered in the future, leave a comment on this page or email me at dzeiger@instituteforsupplymanagement.org.