Inside Supply Management Magazine
September / October 2020
Articles
Industry 4.0: A Practical Guide for Empowering Teams
September 15, 2020
ISM Mastery Model® Core Competency: Project Management
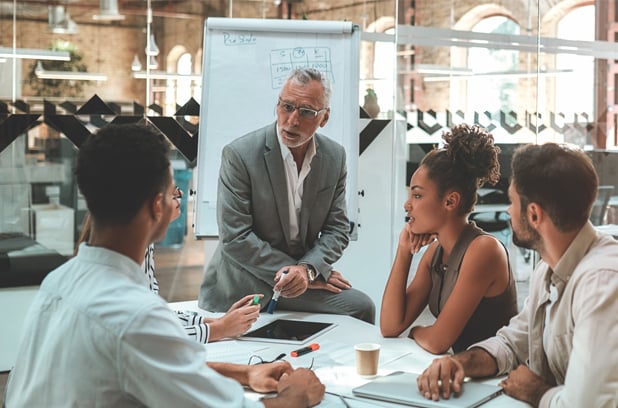
The practical productivity that can be gained through the digitization of manual processes offers organizations exciting cost-savings opportunities to address near-term headwinds. Industry 4.0 technologies can accelerate companies’ digitization strategies by enabling teams to drive greater organizational agility and profitability. Think of these technologies as simply tools that do a job — in this case, software converts manual data into digital data to offer practical productivity gains.
...Want More Magazine?
Oh no... we really want you to have access to all of this great content! Membership does have its benefits and Inside Supply Management magazine is just one piece to help you advance your organization and your career. Learn more and join our community.