Inside Supply Management Magazine
November / December 2020
Articles
Diversifying Mask Supply Amid the Pandemic
November 10, 2020
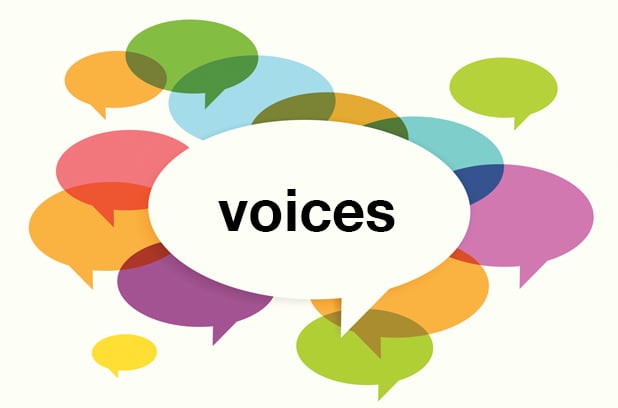
For years, HonorHealth, a nonprofit hospital system based in Scottsdale, Arizona, used only two makes and models of N95 masks for its personnel. But when the coronavirus (COVID-19) pandemic hit and N95 manufacturers could no longer meet the health-care company’s supply demands, HonorHealth — like companies across many industries during the pandemic (see page 40) — diversified its sourcing to ensure adequate supply.
...Want More Magazine?
Oh no... we really want you to have access to all of this great content! Membership does have its benefits and Inside Supply Management magazine is just one piece to help you advance your organization and your career. Learn more and join our community.