A Look Back: Supply Chain Resiliency in the Making
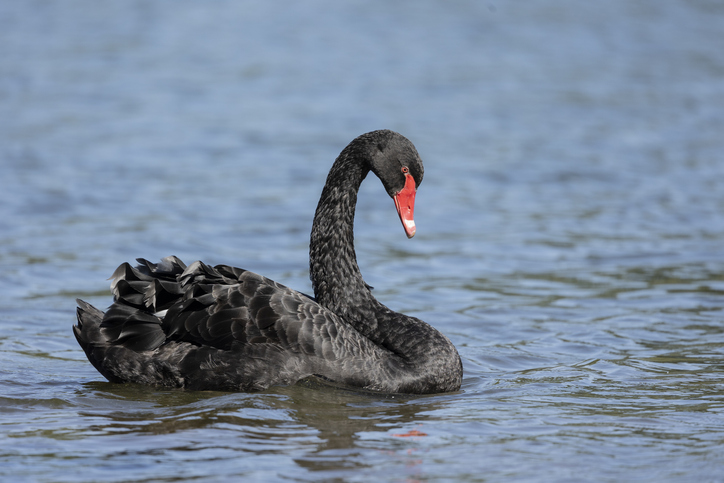
It’s been four years since the start of the coronavirus pandemic, and in that time, supply chain management professionals have learned through experience what it takes for their organizations to be resilient.
Let’s take a look at the disruption they’ve undergone — and where they are now.
The Black Swan
The year began as Wall Street and main street awaited news of robust retail sales numbers for the 2019 holiday season. Trade uncertainty was contributing to slumping manufacturing activity, as the country entered into the first phase of a China-U.S. trade deal, although tariffs levied under then-President Donald Trump remained on many goods. Some believed trade headwinds would continue to impact manufacturing throughout 2020.
As a hedge against the slowdown, global supply chain managers turned to third-party logistics providers, pivoting outsourcing budgets to meet needed increases, according to a Gartner study.
U.S. farmers were unsure of what crops to plant, amid a changing export landscape and China’s push for new supply chains, making future demand planning untenable.
By March, procurement decision-makers were blindsided as the COVID-19 trajectory increased in scope, scale and speed, to an unprepared global economy impacting livelihood and mortality rates. Representatives from food and retail companies shared concerns over possible export restrictions of chemicals, ingredients and other products, a precursor to medical and food supply shortages. What validated retailers’ fears were empty grocery store shelves, feeding customer demand for food and paper goods.
By that summer, the supply chain profession was immersed in irony: the coronavirus pandemic overpowered the world’s economic infrastructure, just as pharmaceutical companies needed to launch “the biggest and most consequential product in modern history,” a Bloomberg article stated. Beyond the urgency of throughput and output, logistics presented further challenges for drug manufacturers due to shrinking container-ship capacity and disruptions along distribution channels.
Manufacturers saw further decay in operations, ailing workers became more prevalent. With lockdowns in place, demand for new vehicles waned. Supply chain disruptions were a chokehold to the automotive industry, and in July, General Motors cancelled Saturday overtime work at a Texas SUV plant, while temporarily shutting production at a Kentucky Corvette plant.
2021
Heading into the following year, coronavirus cases surged across the globe, with daily death toll counts visible on news headlines and the U.S. Centers for Disease Control and Prevention (CDC) website. Imports began to reach Los Angeles and Long Beach ports, a welcome relief to the surge in e-commerce orders. In the first quarter of ’21, the Port of Los Angeles saw a 44-percent rise in 20-foot-equivalent units (TEUs) compared to the first three months of 2020.
Soon after, the tide turned again. One in 10 dock workers at Southern California ports were off the job, citing COVID-19 reasons, causing reduced productivity amid a backlog of more than 100 ships waiting to be unloaded.
America’s railways didn’t fare much better. Union Pacific, covering Los Angeles County, experienced a 160-percent increase in thefts year-to-year since January 2020.
Some economists projected an easing of bottlenecks for 2021, the optimism was met with disappointment as China continued its zero-COVID policy, enforcing strict quarantines and travel restrictions, and prolonging supply chain disruptions.
2022
Russia’s invasion into Ukraine in February was yet another blow to supply chains wrought with tribulations, adding pressure in the sourcing of raw materials, grain and energy. By the third quarter, Russian state-owned energy exporter Gazprom PJSC announced the shutdown of Nord Stream pipeline gas flows to Germany from August 31 to September 2 for safety inspections. As a safeguard, Germany filled its gas storage to near 78 percent of capacity to endure winter.
According to FreightWaves, 2022 was the costliest year on record for the transportation sector, specifically companies that own and manage 18-wheelers. The American Transportation Association (ATA) reported a 12.7 percent year-over-year increase in trucking’s total marginal costs.
2023
Geopolitical strains escalated, decreasing chances for a peaceful resolution between Russia and Ukraine. While attending the Universal Declaration of Human Rights’ 75th anniversary session, United Nations secretary general Antonio Guterres warned 193 member nations to change their global perspectives away from “near-term thinking” to prepare for a wider war.
Global supply chains focused on recovery, coming out from under masks of disruption, while seeking ways to bolster business. Conversations about widespread integration of artificial intelligence (AI) began to emerge. News of IBM’s five-year commitment to AI shook boardrooms and workers worldwide as the company announced that 30 percent of its human resources jobs and other non-customer-facing roles would be replaced by AI.
Meanwhile, American, Southwest and United Airlines pilots sought better compensation, similar to Delta’s new deal, which cost the airline nearly US$7 billion over four years.
Logistics giant DHL forecast a stable peak season for 2023, and anticipated inventories nearing “normal,” a term many industry professionals used with caution, in light of the volatility recently experienced.
Aerospace giant Boeing continued its struggles, with long-haul carrier Emirates cancelling its planned Airbus A350 purchase after worries over its Rolls-Royce engine.
Here and Now
Uncertainty, volatility and insecurity will ebb and flow across time, and so it goes with supply chains. What the past four years have shown — as the coming years will — is when organizations lead with innovation, integrity and a commitment toward the greater good, resiliency follows.